Understanding Industrial Automation in Industry 4.0
Are you excited that the future of American manufacturing is looking brighter due to reshoring? We think it’s great too, but have you noticed something different? Manufacturing has changed. There are new technologies, such as talk of Industry 4.0, robots, co-robots, and the Internet of Things (IoT).
While the U.S. was sidelined by offshoring, other countries were advancing automation technologies to capture maximum efficiencies. American manufacturers will need to play catch-up in order to continue growing and speeding re-shoring opportunities.
If you want to become globally competitive and move into more efficient automation equipment or systems, you will need at least a basic understanding of industrial automation as it stands today. Understanding options, terminology, and components will make it easier to create initial plans and budgets that can be discussed in greater detail with team members and automation solution specialists.
To get you up to speed, here is a basic overview of industrial factory automation in the age of connectivity.
Table of Contents
What is Industrial Automation?
Types of Industrial Automation
How is Industrial Automation Achieved?
Manufacturing Production and Industrial Automation Systems
Why American Manufacturers Need to Automate
Automation in Industry 4.0
Arriving at an Industrial Automation Solution
What is Industrial Automation?
You are not alone in your search for manufacturing efficiencies. Since before the first industrial revolution, industry leaders have created specialized machinery that can produce faster and more precisely than a human with a hand tool. Historically designed to operate independently with minimal human intervention, today’s industrial automation systems can communicate and work in sync with the assistance of industrial control systems and network connectivity.
You will find examples of industrial automation equipment where products or components are machined, manufactured, packaged, and/or assembled. With automation principles and standards, you can expect automated machinery to be placed in a system configuration that most efficiently moves components from one stage to the next.
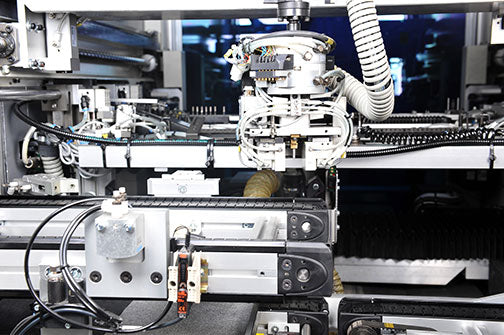
Types of Industrial Automation
Manufacturers are automating jobs that require endurance or precision, or those that are boring, repetitive and/or require little creativity or specialized talent. Decreasing robot costs and increasing labor costs are encouraging automation in the U.S. With robot prices expected to fall by upwards of 65% over the next five years, automation is predicted to rise steadily. If you haven’t already done so, investing in a data communications infrastructure may be one of your biggest challenges. Trending factory automation relies on the ability of machine networks to communicate and enact tasks on schedule.
What are the common types of factory automation?
- Simple tooling
- Assembly
- Inspection
- Materials handling
How is Industrial Automation Achieved?
Industrial control systems are the mechanism (or brain) behind automated machine independence and motion. This is the technology that allows for industrial processes to be automated. The primary make-up of a control system is the control loop. Examples of control systems range from the very simplest, a discrete controller, to the complex SCADA system which manages all levels of a business’s manufacturing processes and geographical locations.
Types of industrial control systems:
- SCADA system - a computer system that controls and monitors plant processes
- Proportional-integral-derivative controller (PID) –controls a system based on set-point and measured value
- Programmable logic controllers (PLC) – an easily programmed, rugged industrial computer with a single microprocessor used to control motors and other machinery in a factory setting using logic
- Programmable automation controllers (PAC) – similar to a PLC, but contains multiprocessors and is capable of multitasking
- Distributed control systems (DCS) – controls many nodes in a system through multiprocessors with advanced capabilities including many I/O points
- Human-machine interface (HMI) – allows you to interact with a machine and quickly view the status of machine processes
- Discrete controller - simple on and off control, examples are timers, counters and thermostats
PLC |
|
Counter |
How industrial automation works:
Stage 1 - The industrial control system (listed above) works in conjunction with the drive controller.
Common drive controllers include:
- Variable frequency drive – an AC motor controller that uses frequency and voltage to control speed and torque electric motor
- Stepper drive – a driver circuit that controls the stepper motor with current delivered in pulses and phases
- Analog-servo – this device controls the speed of the servo motor through on and off voltage signals or pulses
- Digital-servo – like the analog-servo, but capable of delivering a much higher rate of pulses per second
Variable Frequency Drive
|
Stage 2 - The drive controller directs the actuator which imparts motion.
Common actuator types include:
- Hydraulic actuator – fluid pressure moves a piston through a tube to build torque
- Pneumatic actuator – Air or gas pressure is used to control speed and torque
- Electric actuator (AC, DC, Linear, Servo, Stepper) – powered by a motor, electrical energy is converted to mechanical torque
- Mechanical actuator – using simple mechanisms, a rotary motion is used to create a linear motion
Pneumatic Actuators |
Industrial automation continuous processes:
- Feedback sensors (encoders or resolvers) collect data from the load and send it back to the controller.
- Fieldbus and ethernet connections support the exchange of information between basic field devices and can transmit up to the enterprise level.
- Working in conjunction with automated controls are mechanical devices including bearings, gearboxes, screws, wheels, axles, cams, and linkages.
|
|
-
In addition to the electromechanical and mechanical devices, fluid powered machine devices are also utilized in industrial machinery. When electromechanical methods fail to provide practical solutions, fluid power is introduced. Fluid power is typically driven by electronics and controlled by sensors and valves.
Fluid Power Technologies
-
Pneumatics transfer power via compressed gas or air. Pneumatics provide a less costly option to electrical drives when power and speed are required for a machine task. Robotic technology relies heavily on pneumatics for operating end-of arm-tooling and accessories such as grippers.
-
Hydraulics transfer power via liquid pressure. Hydraulics are reserved for machine tasks that require higher forces applied to loads than pneumatic systems can generate.
Linking these components and integrating data, not just on the factory floor but enterprise-wide, creates a single point solution.
The automation communication pyramid visually explains the technology communication links and integration opportunities within a factory:
Manufacturing Production and Industrial Automation Systems
If you are considering automation for your factory floor, the keys to getting a return on your investment include foresight, machine layout, and flexibility. An automation system is a machine layout designed to most efficiently complete a manufacturing process. A manufacturer may need to complete one constant task or have multiple tasks to be completed in an order of operations. The most important aspect of a system is accounting for possible machine changes.
Machine design is determined by answering the following questions:
- Will products be produced by units, in batches, continuously, or in a mass flow production?
- Will stations operate synchronously or asynchronously?
- What is the total number of workstations needed?
- Will the system be linear, rotary indexing or contain both?
Industrial automation system designs fall under three categories:
Fixed or hard automation
Fixed/hard automation is designed for large volume production of a single product or task. The machine layout is designed to the fixed sequence of operations.
Pros—
- Typically, lower build costs compared to programmable and flexible options.
- Improved product consistency
- Operates at high speed for a high production rate
- Lower unit cost for each piece sold
Cons—
- Machine layout inflexible, so alterations to design are costly and time-consuming
Example of fixed automation
Programmable automation
Programmable automation if for the manufacturer that needs flexibility in production for batch runs. Programmable machinery allows for the reprogramming of sequences which will allow for different product configurations.
Pros—
- Flexible system
- Suitable for batch runs from 50 to 1000 units
Cons—
- Re-configuring the system can still be time-consuming.
- This system requires an upfront substantial investment for general purpose programmable equipment.
Flexible or soft automation
Flexible/soft automation is an extension of programmable automation, but with less time lost for reprogramming or tool changes. This automation is for the manufacturer that needs to run a variety of products with no downtime between batches.
Pros—
- Continuous production includes in sequence product variables
- Medium production
Cons—
- Higher initial investment than fixed or programmable
- Components that allow for quick changes, such as a robot arm, will need logic controllers, sensors and lasers.
- Skilled labor for part changes, maintenance, and other supervisory duties.
Why American Manufacturers Need to Automate
Consumer demand and reshoring will continue to drive American manufacturers to seek out faster, more efficient and precise production processes. Consumers want the latest, greatest product as soon as possible at the lowest cost and with the highest quality. On top of consumer pressures, offshoring is proving to be costlier than expected.
With reshoring, American manufacturers are having to play industrial automation catch-up. The pace of American automation has been slower to that of competitors from South Korea, Singapore, Germany, and Japan. American manufacturers don’t want to fall further behind in automation technology, but instead, lead the way. Between consumer confidence and global leveling, manufacturing confidence is running high in America once again.
Graph Reference: 2019, Raconteur, Age of Automation
Why is reshoring trending?
- Rising transportation and shipping costs
- Rising labor costs
- Quality control issues
- Tariffs
- A desire to reinvest in the American economy
- U.S. trend toward factory automatization and robotization
Automation in Industry 4.0
Each period of industrial progress has been ushered in with new ideas and technology. Water and steam-propelled us into the first industrial age, the second was ushered in by the assembly line and electricity, and the third, a precursor to the fourth, was the birth of the computer age.
The fourth industrial revolution, or Industry 4.0, is upon us and it's being driven by data communications. Smart factories are utilizing cloud-connected devices from the Internet of Things (IoT) to monitor everything from machine processes to inventory levels. In a factory, IoT devices interconnect machines and cyber-physical systems allowing for real-time data transfers, monitoring, and control. Globally, industry manufacturers are adding smart factory initiatives to their formal goals and objectives.
Efficiencies captured from an Industry 4.0 smart factory include:
- Increasing productivity
- Improving quality throughput and output
- Reducing labor costs
- Reducing the impact of labor shortages
- Decreasing safety concerns in hazardous environments or those with repetitive tasks
Arriving at an Industrial Automation Solution
Before initiating an automation order, you will want to thoughtfully consider new and emerging technology options in relation to existing and foreseeable needs. Efficiencies are only captured if the new automation performs as expected with no surprises. Whether automating an entire factory or only a portion, important considerations include the need for skilled labor to run or maintain equipment and a machine design based on realistic expectations. A custom automation expert can reduce errors in design and enhance areas that reduce waste and improve quality.
Custom automation providers are helping American manufacturers capture efficiencies with one turnkey machine or with factory wide solutions that include robots and other Industry 4.0 technology. Working with manufacturers, a custom automation expert will evaluate a process and make system design recommendations to avoid or correct problems such as production bottlenecks or potential safety issues. Solutions can be either fully automated or semi-automated with an eye toward the future and changing needs.
A quality industrial automation expert will have the following capabilities:
- Portfolio of successful manufacturing automation experience
- ISO 9001:2015 Certification
- Authorized Robotic System Integrator
- Offers Turnkey solutions
- A website with valuable industry information
What’s Your Conclusion?
While you may have automated equipment that represents the best craftsmanship of the by-gone era, it is still considered antiquated in comparison to the efficiency standards of today’s players. Is it necessary to invest in updated automation technology?
The answer can be seen in the actions of those countries dominating in automated manufacturing. They aren’t just using existing technology to gain efficiencies; they are using technology innovations to gain competitive advantages. The use of artificial intelligence (AI) is ushering in a new generation of collaborative robots. To stay on top, Korean investors will most likely be the early adopters of this new technology.
Don’t be discouraged if you are just entering this market. A little change can go a long way in capturing efficiencies and late is better than never. To make American manufacturing great again, it is going to take innovative thinking and investment like that seen in the American industrial revolution.
Was this overview helpful? If you have any follow-up questions or want to discuss your automation needs in detail with an expert, give us a call, (866) 351-4901, or send us an RFQ today! We would love to hear from you.